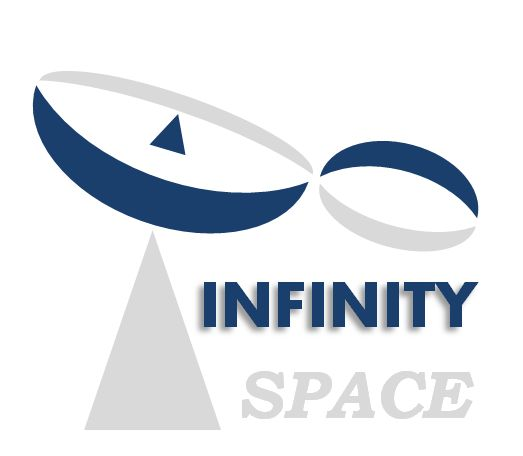
The primary subsystems contained within the lander are the communication system, motors and electronics used for steering the antenna, a microprocessor system for command and data handling, and the various sensors that perform the data collection task of the mission. The estimated power budget of each electronic subsystem is shown in the table below.
Subsystem | Power budget |
---|---|
Communication subsystem | 285W |
Antenna Steerig | 50W |
C&DH | 30W |
Sensors | 20W |
Total | 385W |
The communication power is derived from the 200W transmitter power, to which we add an efficiency of 0.7 in the TWTA [46]. The antenna steering power is from [45].
Considering the exterme environmental condtions on Venus [38], any mission to Venus must provide adequate thermal control in addition to using high-temperature and high-pressure electronics. Our lander utilizes a two-stage Stirling machine system for both power generation and active cooling [1]. The Stirling machine used on our lander is an example of a radiosotope power system (RPS), which generates power from the radioactive decay of plutonium. The RPS uses general purpose heat source (GPHS) modules, each of which contains close to 0.6 kg of plutonium [38], to produce a large amount of heat, which the Stirling engine uses to generate electricity. Although Stirling generators have achieved efficiencies of over 25%, we conservatively estimate the effieciency to be 20% [1]. Each GPHS module can produce 250W of thermal power, which can then be converted to 50W of electrical power.
Our cooling system requires 72 GPHS modules to refrigerate the inner vessel of the lander. The total power budget of our lander’s electronic subsystems is conservatively estimated at 375W. Thus, we require an additional 8 GPHS modules to generate up to 400W of electricity. Our power system is estimated to weigh 162 kg, consisting of 128 kg of GPHS modules and 34 kg for the Stirling engine.
Although RPS and RTG systems have been successfully used in space missions for many years, our RPS will be re-designed to withstand the harsh conditions on Venus. Improved heat rejection and heat-tolerent components must be used to survive the 460 degree surface temperture. The RPS will also need coating in order to tolerate the corrosive supercritcal carbon dioxide environment [38]. We estimate that the overall cost of our power system will be $80 million. Our RPS will be higher than previous RPS and RTG systems due to the many required design changes [39].
Desipite the higher cost and political considerations, it is necessary for this mission to use an RPS. The Stirling RPS in our lander is capable of supplying full power to our electronics and cooling system, regardless of altitude. Due to the 87-year half line of plutonium-238, an RPS is effectively an unlimited source of power for our mission to Venus.
Using solar panels on the surface of Venus is not a solution. Indeed, as explained before, the solar flux is very low. But also, at the high temperature, current solar panel technology has a very poor efficiency, especially in the spectrum not filtered out by the atmosphere [21].
Using Lithium-thionyl chloride batteries, which provide 477 W-hour per kg [1] would not be reasonable either, because we would need more than 500kg of batteries.